Operations Director - Construction Products Manufacturer
Collingwood were approached by this construction product manufacturer of cementitious materials to secure an Operations Director.
Part of a wider Group, which includes household brands from within the industry, the Group turns over £300m globally.
They satisfy an abundance of markets to include the specification, retail, housing developers and consumer markets
Over the past six years this individual manufacturer has trebled turnover and are diversifying into new product ranges, with a hardened business strategy in place to push revenue figures to more than double turnover inside the next five years.

The Role & Its Challenges
The site was in the third phase of a £1m plant upgrade. This would double the capacity of the main line, with the incoming person taking ownership of this.
The dramatic growth had come at a cost, with a stretched operational side. This person would take immediate ownership of improving servicing levels and on time in full metrics.
Additional focus included:
- Taking ownership of developing the operational strategy and associated KPI setting
- Mentoring a new Production Supervisor
- Gaining maximum return on an ERP and bar code scanning system introduced two years ago.
- Driving a more continuous improvement and accountability mind-set at operative level
Due to budgetary constraints, this client had a defined salary structure in mind. Collingwood’s Head of Building Products, Mark Goldsmith, stated that the company was 15-20% short on the basic salary against market rates.
Mark therefore suggested approaching Operation / Factory and Plant Managers who, through assessment, are deemed ready for the step up. This allowed the client to sell this position at an Operations Director Designate level, with agreeing firm metrics and stage gates being agreed early into their tenure to move it into a bona fide boardroom role.
Upon agreement, Collingwood were to research individuals from a “blending” orientated manufacturing process (raw material in, finished product out), where an appreciation of the pressures associated with running continual lines is paramount.
About the author
With 25 years of recruitment experience under his belt, Mark has spent the last 21 focused on Building Products & Construction.
Read more >Share
The Solution & Result
Mark advised the client that there would be little need to offer relocation for this level of position and thus started researching companies located within a 50 miles radius of their plant.
He advised on six sectors that would align to this continual process style of manufacturing and, once agreed with the MD, researched companies from these, leading to 47 potential targets.
Some larger sites had two potential targets, leading to a total of 61 individuals. Collingwood also developed a social media campaign to draw interest from their extensive network built within building products.
Through weekly updates with the MD, Mark shaped the interested parties down to five to assess in full. Three were recommended and interviewed by the client; two progressing to second stage. The preferred candidate then met with the rest of the board, along with the Group CEO, with Mark managing the offer and notice period process through to starting. The preferred candidate had been working as a Plant Manager within a bakery setting.
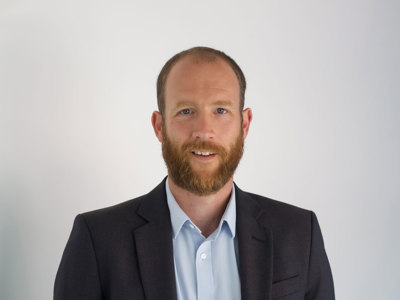